Technical services
Design of custom parts, reverse engineering and production of parts in technical materials are just some of the technical services provided by Actualizings.
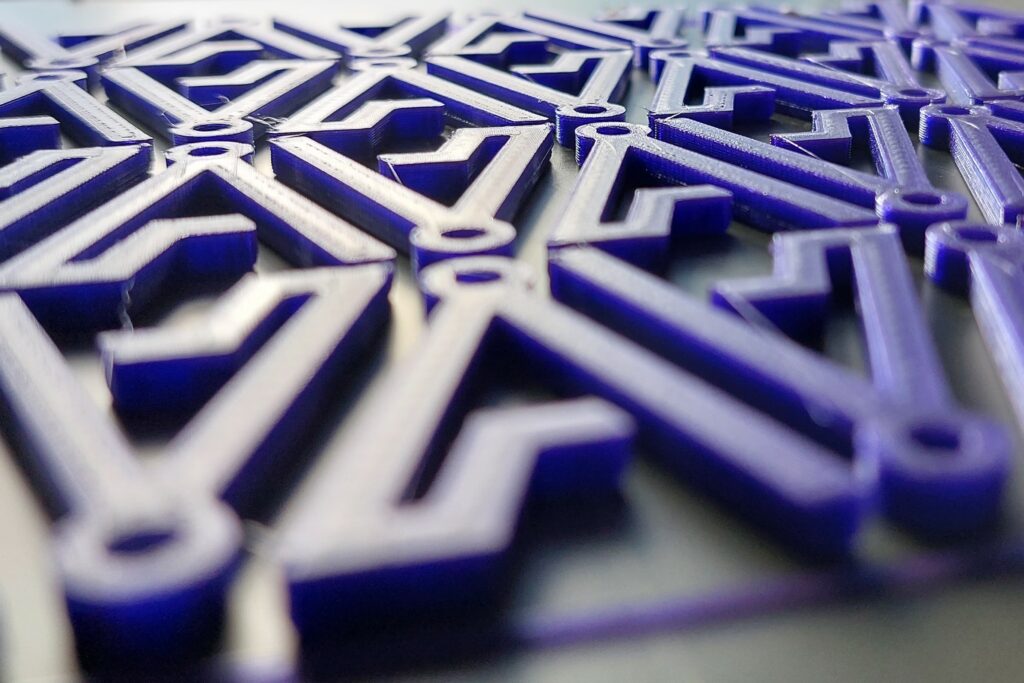
Low to high volume production runs
3D-printing can provide low volume production runs where injection molding is too expensive, as low as 1 piece. At the same time production can scale up to hundreds of parts without losing the ability to switch to a new part iteration at any time without significant production delays or unexpected costs.
One of our Technical realizations
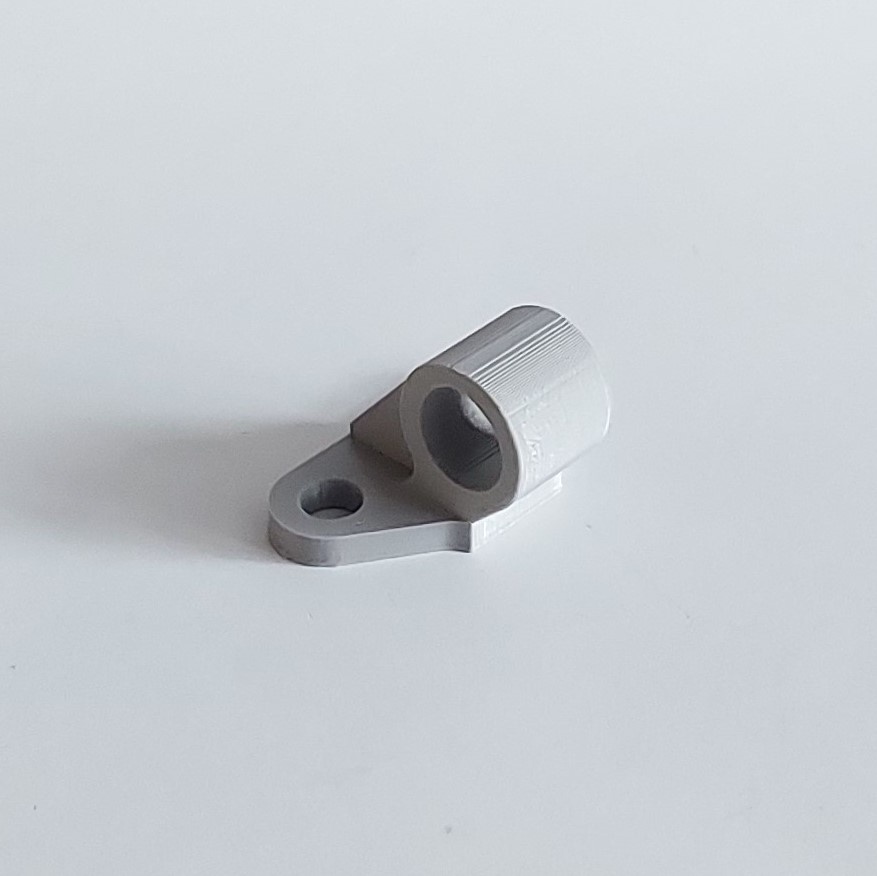
Functional re-productions
Based on original parts designs where created for parts of the throttle shaft mounting. The parts are produced in PolyCarbonate to meet the required heat, wear and strength requirements.
Our materials
Different projects and parts require different materials to bring them to their full potential. That’s why parts can be produced in a range of materials, to match your needs.
Below you can find a limited list of the supported materials. Others materials can also be made available on request.
PETG - Economical, most popular option
PETG shares many charasteristics with the more commonly know PET material, although PETG has slightly lower temperature stability, with decreased strength starting at 70 °C.
PETG strikes a good balance between cost and techincal characteristics which makes it one of our most often recommended materials.
Recommended use
With its mix of technical characteristics and low cost, PETG is our go-to material unless specific characteristics are required.
ASA/ABS - high temperature and impact resistance
ASA is in many ways the successor to ABS, improving in the areas of temperature stability, tensile strength and impact resistance.
Recommended use
When more impact resistance is required than available with PETG.
PC (PolyCarbonate), great tenacity, tensile strength, and heat resistance
One of the strongest materials available in our portfolio.
Outside of the 3D printing world, polycarbonates are used for making CDs, protective glasses and shields, or car headlight covers.
Retains most of its strength up until 110 °C.
Recommended use
For situations with high technical requirements at an increased cost.
Flexible materials TPU/TPE
Ranging from TPU to TPE, multiple flexible materials are available with different hardness.
Nylon PA6, PA11-12 - Strength and great wear resistance
Our most wear-resistant material. Nylon’s have great strength and heat and wear resistance. Nylon can often be used to replace existing metal parts.
3D printing also allows the usage of composite nylons with carbon or glass fibers, providing even greater strength and wear resistance.
Composite materials
Composite materials (PLA, PETG, PC, or ABS filled with carbon, kevlar etc.) usually have better mechanical properties than unaltered filaments.
They can also replicate tactile sensations as provided by metal and wooden parts.
Interested in our service?
Feel free to reach out to for a quote, to set up a conversation on how we can best help you with our services or any other information at:
© 2022 All Rights Reserved.
Address
Krekelstraat 72, 8770 Ingelmunster
Contact
Tel +32 471 24 49 92
Email info@actualizings.com
Enterprise number
0795212532